A kontraszt szerepe a nyomtatás minőségi ellenőrzésének folyamatában - a nyomtatási folyamat
Jelentősen megnövekedett a nyomtatott termékek minősége, többek között a nyomdaipari berendezések - előkészítő, nyomdai és befejezési - park folyamatos fejlesztése. A megrendelések minőségére vonatkozó magasabb acél- és vevői követelmények. Ha korábban az egyik legfontosabb követelmény az volt, hogy átfedik a benyomást (és nem különös figyelmet fordítanak mindenre), ma az ügyfél egyértelmű, gazdag, "élő" képet akar. Az ilyen házasság, mint az otmaryvanie, a nyomtatás hiánya, "liba-dudorok" stb., Ma egyáltalán nem tárgyalták.
A fő minőségi kritérium - az eredeti (színes bizonyítékok) reprodukálásának pontossága - a fő paraméterek határozzák meg: fizikai, kolorimetrikus és pszichológiai. Szinte lehetetlen megszüntetni a színeltérés és a benyomás közötti ellentmondást. Ez a következő okok miatt következett be:
- A benyomás más anyagból készül, mint az eredeti;
- a benyomást más színezékek felhasználásával végzik (mivel az eredeti színek spektrális jellemzői és a benyomást keltő színek nem ugyanazok, csak bizonyos fényviszonyok között lehet a színazonosság);
- az optikai sűrűség az eredeti és a nyomtatott színcsatornákon eltérő, ami viszont eltérő színvisszaadást eredményez. De még akkor is, ha bevalljuk, hogy a színmérés tekintetében a színek egybeesését el fogják érni, még mindig léteznek pszichológiai tényezők, amelyek még mindig nem teszik lehetővé az abszolút egybeesést.
Ábra. 1. A nyomtatási folyamat működési ellenőrzési skálái:
a tetején - "csökkentett", alul - további
vezérlő mezők
A kiváló minőségű termékek beszerzésének legfőbb feltétele az összes technológiai követelmény teljesítése. És csak a termelés minden területén történő gondos ellenőrzése - a fogyóeszközök kézhezvételétől a forgalomba kerülő csomagolásig - valóságos minőségű lesz.
Mindazonáltal a nyomtatási folyamat vezető szerepet játszik a nyomdaiparban. Milyen kritériumok vannak a nyomatok minőségének meghatározására? Mit tart a nyomtató, a mester vagy a technológus a nyomtatási folyamat ellenőrzése során?
Ábra. 2. Kombinált skála, amely lehetővé teszi a vezérlést
különböző nyomtatási lehetőségek
A nyomtatási folyamat szerepe
A poligráfia modern fejlődési stádiumának érdekessége - a szakemberek túlnyomó többsége kiemelt figyelmet szentel az előkészítő folyamatoknak. A legfejlettebb kimeneti eszközök (amelyek nagyon hosszúak és finoman kalibráltak), csúcskategóriás szkennerek és digitális fényképezőgépek, drága kalibrált monitorok használatosak. És mindezt annak érdekében, hogy az eredeti "gyönyörű" százaléka minden alapszínre, ami az "azonos" színvisszaadást biztosítja.
És most, miután ezeket a „kínzás” a film utal, hogy a nyomtatót, és várjon beszerzésének „hogy” az ígért eredményt. Azonban a nyomtatás eredménye meglehetősen váratlan lehet. Az a tény, hogy a nyomda hatalmas mennyiségű különböző beállításokat és beállításokat tartalmaz. Mind az általános és zonális tintabevezető is széles határok között változhat, és ha hozzátesszük kiigazítási ellátó gátló- vagy nyomása különböző részein a gép, a számát nyomtatási eredményeket lehet elérni ugyanolyan alakú lesz végtelen. Ugyanakkor, amint az a cikkben helyesen szerepel, az alaplemezek optikai sűrűsége elfogadható szinten lehet. Ezért minőségi és kiszámítható eredmény csak akkor érhető el, ha a nyomda számos nyomtatási paramétert vezérel.
Van egy másik szélsőséges - ha ismert, hogy a folyamat a nyomtatás színvisszaadást szabályozza, lehetséges, különösen nem „törzs”, hogy prepress imaging „nyomtatásban utánállító.” Azonban meg kell érteni, hogy nem minden "beállítható". Például, ha egy lapon egy kép kell hozzá „vörös”, és egy másik - a „kis kék”, ez nem működik - akkor csak egy dolgot, és akkor is csak egy kis tartományban.
Ezért próbálják szabványosítani és felhasználni ugyanazokat a nyomtatási paramétereket a világ minden táján - mind az előkészítési szakaszban, mind közvetlenül a nyomtatási folyamatban. Csak azt kell figyelembe venni, hogy ha viszonylag könnyű követni a szabványokat a préselőszakaszban, akkor nagyon nehéz megtartani őket a nyomtatási folyamatban (hatalmas számú beállítható paraméterrel). Ezért kell a nyomtatási folyamatot a végtermék minőségének biztosításában legfontosabbnak tekinteni.
Az emberi szem hiányossága ismert, és a nyomtatásban ez nagy jelentőségű. A műszerek használata a munkafolyamatban a termelés szerves részévé vált. Eljutott az idő, amikor egy drága denzitométer támogatott vagy terhelést jelentett a kontroll benyomásoknak. Az ellenőrző és mérőberendezések lehetővé teszik a gyártási folyamat hibáinak azonosítását és korrigálását. Nem szabad elfelejtenünk, hogy az eszközöket teljes mértékben ki kell használniuk a benne rejlő funkcióknak. Ismételten kellett foglalkoznia egy ilyen helyzetgel, amikor az ügyfél továbbra is elégedetlen volt a nyomtatás minőségével, például a képek telítetlenségéről beszélt. A probléma megoldása érdekében a denzitométer 100 százalékkal meghaladja az ellenőrző benyomódásokat és azok összehangolását az offszet nyomtatás színvonalával. Ha az összes jelzés megfelel a megállapított normáknak, akkor a nyomda képviselője felemeli a kezét, és azt állítja, hogy a nyomtató a megfelelő minőségű munkát végezte el, - az ügyfél kénytelen elfogadni a nyomtatási feladatot, és okleveleket keresni előkészítő munkákként.
Ábra. 3. A különböző pontértékű képek:
a) normális, b) kissé túlértékelt, c) túl magas ár
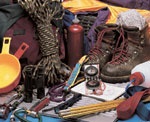
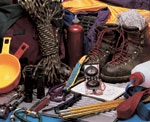
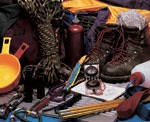
Pontosan az ellenőrzési benyomások ellenőrzése és a denzitométeres mérések munkája során szeretnék külön figyelmet fordítani. Minden nyomda a működési ellenőrző mérlegeket használja a nyomtatási folyamat ellenőrzésére, de gyakran ezek a mérlegek csak 100 százalékos alapszínű szerszámokból állnak (1. ábra), ami helytelen.
Definíció szerint az ellenőrzési skála olyan normalizált tesztelemek készlete, amelyek a nyomdai eljárás különböző paramétereinek minőségét nyomon követik és értékelik. A modern mérlegek számos olyan mezőt tartalmaznak, amelyek lehetővé teszik a különféle nyomtatási paraméterek szabályozását, pl. 2.
Ha egy "egyszerűsített" skálát használunk, a tinta alkalmazásának ellenőrzésére, a szürke egyensúlyra, a raszterelemek raszteresedésére, a csúszáskor, illesztésre stb.
Spatting - növeli a nyomtatási raszter pont méretét a nyomtatás során az érintkezési zónában lévő megnövekedett nyomás miatt. Ez hatással van a színvisszaadásra, különösen olyan esetekben, amikor a színt több szín bevetésével alakítják ki. A nyújthatóság természetes, ami elkerülhetetlen az offszetnyomtatásban, és másodlagos - ez a technológia megsértése és a nyomda helytelen beállítása miatt következett be.
Ez a növekedés lehetővé teszi számunkra, hogy megítéljünk egy olyan koncepciót, mint a nyomtatás kontrasztja. Kontrasztnyomtatás - az árnyékolással meghatározott érték, amint a raszterpont megközelíti az optikai töltést. Ez az érték magyarázza a kép zavarosságát és telítetlenségét, miközben figyeli a 100 százalékos lemezek optikai sűrűségének denzitometriás szabványait. Az 1. ábrán. A 3. ábra három, különböző pontértékű értéket mutat: normál, enyhén és erősen túlárazott. Könnyű látni, hogy ahogy a ponterősítés nő, a kép elveszti természetes, "élő" megjelenését. Ebben az esetben a vizsgálati lemezek optikai sűrűsége minden esetben megegyezik.
A nyomdagép felállításának módja
A technológia a következő: nagyon telített benyomást kelt, vastagabb festékréteget kell alkalmazni. Azonban, amint a tintaréteg vastagsága megnő, a ponterősítés nagyobb lesz, és a kép reprodukciós minősége csökken. Felmerül a kérdés: mennyi ideig tudom növelni a festékáramlást, amíg pozitív hatással van a színvisszaadásra?
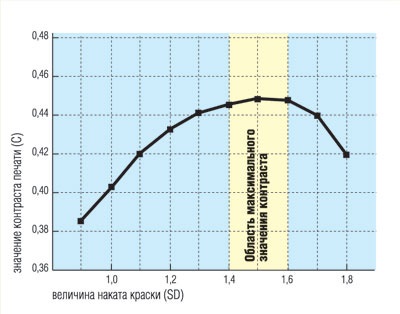
Kiderült, hogy a nyomtatási kontraszt jó mutató. Fokozatosan növeli a tintabevonást, végez több mérést a nyomtatás kontrasztjával. Ezután rajzolja be a diagramot: egy tengely - a festékhenger mennyisége, a másik - a nyomtatási kontraszt eredményének értéke (ábra). A festékáramlás növekedésével a kontraszt először nő, majd stabilizálódik, majd csökkenni kezd. A kontraszt legmagasabb értékének területén a festékhenger és a ponterősítés aránya a legmegfelelőbb az adott gép számára. Ha ezt az értéket egy adott nyomdaipari vállalat szabványának tekintjük, akkor lehetõség nyílik megbízhatóan beszerezni a nagyon gazdag és élénk nyomatokat. Ezeket a paramétereket figyelembe kell venni az előkészítés szakaszában.
Jelenleg a nyomdák az offsetnyomás optikai sűrűségeire és az elfogadható pontértékre vonatkozó mutatókra támaszkodnak, amelyek átlagértékét a táblázat tartalmazza. 1 különböző típusú papírok esetében. A táblázatban megadott adatokból. 1, Murray-Davis szerint:
A szükséges optikai sűrűséget 80 százalékos raszter mezőre számoljuk. Az "árvíz" kockák standard sűrűségének ismeretében kiszámíthatja a nyomtatási kontrasztot (C):
ahol SD a töltés optikai sűrűsége,
DD a raszter optikai sűrűsége.
Az 1. táblázat adataiból. 1 (tolerancia eltérések), a nyomtatási kontraszt felső és alsó határait számítják ki. 2. Ha a nyomtatási kontraszt értéke fordítottan arányos a raszter optikai sűrűségének értékével, akkor a nyomtatási kontrasztértékek és a ponterősítés közötti inverz arányosság lesz (4.
Táblázat. 1 és Tab. 2
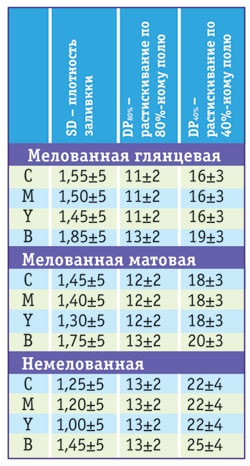
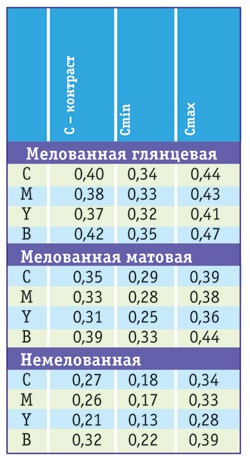
Nagyon fontos a nyomtatás kontrasztjának ellenőrzése a munka során. Az adott értékek közötti jelentős különbségek miatt a nyomtatónak gondolnia kell a nyomtatási folyamatok megváltoztatására.
A sajtóban a kontraszt lecsökkenése esetén a raszterpontok közötti fehér tér fokozatosan megtelik a harmadik féltől származó elemekkel (a ponterősítés növekedése) - az offszet gumi és nyomólemez fokozatosan szennyezett, és mosásra van szükség.
Ábra. 4. Kontraszt és
raszter optikai sűrűsége
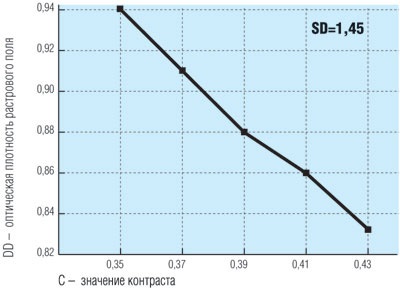
Alulbecsült kontraszt fordulhat elő a takaró és a nyomóhenger közötti túlbecsült nyomás esetén. Ebben az esetben a fedélzeti anyag vastagságát és állapotát ellenőrizni kell. Ajánlatos egy félig merev vagy kemény csomagot telepíteni. Ezenkívül a nyomtatott anyag vastagságát helyesen kell beállítani. Ha kisebb vastagság van beállítva, előfordulhat, hogy hiányzik a nyomtatás, és ha igen, a pontgyarapodás növekedni fog, és a nyomtatási kontraszt csökken. Ezenkívül a kontrasztot az alak és az offset henger közötti nyomás is befolyásolja, a túlnyomás pedig csúszáshoz vezet, és ennek következtében megnöveli a pont nyereségét.
Fontos szerepet játszik a munkában használt festék. Ugyanaz a különböző hőmérsékletű festék diffundálhat különböző módon, így megváltoztatva a raszterpont alakját és méretét. Nagyon gyakran nem elegendő, hogy kompenzálja a szélessége az érintkező sáv növeli a nyomást a roll-off görgők, és ez vezet a hőképződés működés közben (nem lehet elfelejteni a kopás hengerek) és a, illetve festék fűtött, és amely megnöveli a fluiditást (viszkozitás csökken). Megváltoztatásának egyik okát a festék áramlását lehet használni a folyamat további adalékanyagok (például szárítószerek), amely szerepelhet hígítószerként.
A nyomtatás kontrasztjának csökkentése növelheti a festékkínálatot. Ebben az esetben ellenőrizni kell, hogy az offset gumilemez lemezen festett-e réteg. Ennek oka lehet a festék megnövekedett tapadása az alacsony hőmérséklet miatt vagy nagy mennyiségű papírpor belélegzése.
A legtöbb esetben a festék / víz egyensúly megsértése a kontraszt növekedéséhez vezet. különösen a nyomtatás során a vízellátás növekedése. Általában a kontraszt túlbecsülése a sajtó elején figyelhető meg, és ha nem veszi figyelembe az időt, akkor a festék fixen rögzülhet, és ott lesz az oka - túlságosan nagy mennyiségű víz megnehezíti a festék rögzítését. Ez akkor történik, ha a kontraszt legfeljebb 20% -kal nő. Ellenkező esetben az előzetes nyomtatási folyamatra figyelni kell - a lemezek expozíciós módjait megsértették. Ezután hiányzik a nyomtatási elemek, valamint a képek jelentős "szemcséssége".
Mindenesetre az egyes nyomdáknak meg kell felelniük a saját minőségi követelményeinek, a terméktípusok, a felhasznált anyagok és a termelési feltételek alapján. A nemzetközi követelmények és szabványok kiindulási pontot jelentenek a további számlálás és a belső normák kidolgozásának.