Vágó kezelés
Forgácsolás a forgácsolás egy univerzális módja a térbeli feldolgozásnak. A módszer lehetővé teszi különböző alakú és méretű alkatrészek felületének feldolgozását a legelterjedtebb építőanyagoktól nagy pontossággal. Alacsony energiafelhasználása és nagy teljesítménye. Ennek eredményeként a forgácsolás a megmunkálás az ipar leggyakoribb alkatrészeinek dimenziós feldolgozásának fő folyamata.
A feldolgozási módszerek lényege és tervei
A vágási feldolgozás során a technikai állomány anyagának mechanikai vágása miatt a munkadarab felületein forgácsolt darabolással (1.1. Ábra) a kívánt geometriai alakot, dimenziós pontosságot, relatív helyet és felületi érdességet részletezik.
A szerszám egyik fő vágóeleme a vágó ék (1.1. Ábra, a). Keménysége és szilárdsága jelentősen meghaladja a feldolgozandó anyag keménységét és szilárdságát, biztosítva a vágási tulajdonságait. Az anyagnak a vágással szembeni ellenállóképességével megegyező vágóerőt kell felhordani a szerszámra, és a munkadarabhoz viszonyított mozgást sebességgel # 957; Az alkalmazott erő alatt a vágó ék a munkadarabba vág, és a feldolgozandó anyag megtörésével a forgácsokat levágja a munkadarab felületéről. A forgácsok az anyag tömörítésének intenzív elasztoplasztikus alakváltozása következtében alakulnak ki, ami a forgácsolóélben történő megsemmisítéséhez vezet, és a legnagyobb tangenciális feszültségek tartományában a szögben # 966; érték # 966; a feldolgozandó anyag vágási paramétereitől és tulajdonságaitól függ. Ez az
30 ° a szerszám mozgásának irányára.
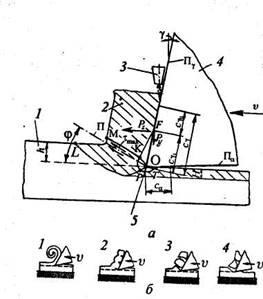
Az apríték megjelenése jellemzi az anyag deformációjának és megsemmisítésének folyamatait, amelyek a vágás során előfordulnak. Négy lehetséges alakú kialakított forgács: a törés, az ízület, az elem és a darabolás (Fig. 1.1, b).
Ábra. 1.1. A vágási folyamat feltételes rendszere:
a - 1 - feldolgozott anyag; 2 - forgács; 3 - kenő-hűtő anyagok szállítása; 4 - vágó ék; 5 - vágóél; # 966; - nyírási szög, amely a hagyományos vágási síkra (П) viszonyított helyzetét jellemzi; # 947; - a vágó ék fő elülső szöge; Pz a vágóerő; Py a normál szerszámnyomás ereje az anyagon; C # 947; C # 947; l - műanyag és rugalmas érintkezők; C # 947; Ca az érintkezési kölcsönhatások zónáinak hossza az eszköz elülső és hátsó felületén; LOM - a fő elasztoplasztikus deformáció területe a forgácsképződés során; FKPT - a másodlagos kontaktus elasztikus-műanyag deformációjának területe fém; h - vágási mélység; H a műanyag deformáció zónájának vastagsága (kemény munka).
A vágási folyamat során a vágási ék, amely intenzív súrlódásnak van kitéve, érintkezik a csiszolóanyaggal és a kezelt felület az érintkezési zónákkal. A súrlódási erők csökkentése és a szerszám felforrása érdekében a kenési hűtő hűtőközeg (SOS) kényszerű hűtését a vágási zónát speciális berendezésekkel ellátva biztosítják.
Az alkatrészeket és a szerszámokat speciális szerszámgépekbe vagy eszközökbe rögzítik. A gép, a szerszám, a szerszám és a rész egy áramellátó rendszert (AIDS) képez, ami erőt és forgácsolást eredményez a gépjármű hajtásától a forgácsolószerszámhoz és a részekhez.
A különböző forgácsolási módok, az alkalmazott szerszám, valamint a szerszám és a munkadarab mozgatásának típusai a feldolgozás során valós képet mutatnak. 1.2. A használt szerszám típusától függően a megmunkálási módszerek lapátra és csiszolóra vannak osztva.
Ábra. 1.2. Vágási módszerek:
a - esztergálás; b - fúrás; c - marás; d - gyalulás; d - áthúzás; e - csiszolás; ж - honing; h - szupervízelés; Dr. a fő vágási mozgás; Ds a feed mozgás; Ro - megmunkált felület; R - vágófelület; ROP - kezelt felület; 1 - esztergáló szerszám; 2 - fúró; 3 - marószerszám; 4 - gyaluipari eszköz; 5 - áthúzás; 6 - csiszoló kerék; 7 - hon; 8 - rúd; 9 - a fej.
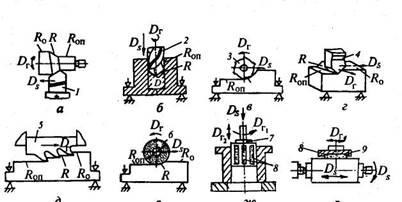
A penge feldolgozásának megkülönböztető jellemzője a feldolgozott eszközben meghatározott geometriai alakú éles élek jelenléte, valamint a csiszolószerszám feldolgozásához egy csiszolószerszám különféleképpen orientált vágószemei, amelyek mindegyike mikroklinus.
Ábra. 1.3. A vágókések tervezése és elemei:
a - esztergáló szerszám; b - vágók; c - fúrók;
1 - a fő vágóél; 2 - a fő hátsó felület; 3 - a penge teteje; 4 - a penge kiegészítő hátsó felülete; 5 - segéd vágóél; 6 - elülső felület; 7 - a szerszám rögzítő része.
Tekintsük a vágás során alkalmazott pengeeszközök kialakítását (1.3. Ábra). A szerszám egy munkadarabból áll, beleértve a vágólapátokat, amelyek a felületüket, vágóéleiket és a gép munkadarabjaiba történő beszerelésre és rögzítésre szánt rögzítőelemeket tartalmaznak.
A fűrészlap feldolgozásának fő módjai a forgatás, a fúrás, az őrlés, a gyalulás és a feszítés. A csiszolóanyag-feldolgozás magában foglalja az őrlési, csiszolási és szupervízelési folyamatokat. A megmunkálás módszereinek osztályozása az alkalmazott szerszám típusától és a mozgások kinematikájától függ. Így, mint egy szerszám fordult használják eszterga vágó, fúró - a fúró, a marás - marás, gyalulás - gyalulás vágó, ha meghúzzák - szóba, ha köszörülés - köszörűkő, hónolás - hones és superfinish - csiszoló rudak. Bármelyik kezelési módszer két mozgást tartalmaz (1.2. Ábra): A legfontosabb dolog a Dr - és a segédmozgás - a segédmozgás - Ds. A fő mozgás biztosítja a fém eltávolítását, és a segédmozgás biztosítja a munkadarab következő kezeletlen szakaszát a feldolgozó zónára. Ezeket a mozgásokat a munkadarab vagy a szerszám mozgatásával végezzük. Ezért a szerszám mozgásának értékelésénél az összes vágási folyamat során célszerű figyelembe venni az összes munkadarabot rögzített üresen (1.4. Ábra).

Ábra. 1.4. A szerszám maximális forgácsolási sebességének meghatározására szolgáló rendszerek # 965; az R vágófelület alakja és a vágási mélység h megmunkálás közben:
a - esztergálás; b - fúrás; in - marás; r - gyalulás; húzással; e - honing; g - szupervízelés.
Ezután a Milling Edge tetszőleges pontjának teljes elmozdulási sebessége (ve) a fő mozgás (v) sebességéből és az előtolási sebesség (vs) összegzéséből áll:
Az R vágófelület olyan felület, amelyet a forgácsolóél vagy a szemcse a teljes mozgás végrehajtásakor ír le, beleértve a fő mozgást és az előtolás mozgását. A forgácsolás, fúrás, őrlés, köszörülés, forgácsolás és húzás esetén - a sík felület, amely egybeesik a fő mozgás felületével; Hegesztés és szupervízelés esetén egybeesnek a fő mozgás felületével.
A Ro és Ro felületeket hívják a munkadarab munkadarab felületére és a munkadarab felületére (lásd az 1.2. Ábrát).
Az esztergálás, fúrás, őrlés és őrlés folyamata során a fő mozgást és a takarmánymozgást egyidejűleg hajtják végre, és a gyalulásnál, a hegesztésnél az előtolás a fő mozgás után történik.
2. A vágási technológiai folyamat paraméterei
A vágási mód fő paraméterei közé tartozik a fő vágási mozgás sebessége, az előtolás és a vágás mélysége.
A fő forgácsolási mozgás (vagy vágási sebesség) sebességét a szerszám vágóélének fő mozgásának legnagyobb lineáris sebessége határozza meg. Ezt a sebességet m / s-ban fejezzük ki.
Ha a fő vágási forgómozgást, mint esztergálás, fúrás, marás és csiszolás, a vágási sebesség határozza meg a lineáris sebesség a fő mozgás legtávolabb van a forgástengelye a vágóéi pontok - a maximális lineáris sebessége a fő mozgás (lásd 1.4 ábra ..):
ahol D a munkadarab munkadarab felülete maximális átmérője, amely meghatározza a forgástengelytől legtávolabbi forgácsolóél pontját, m; # 969; - szögsebesség, rad / s.
A szögsebesség kifejezése # 969; a gép orsósebességén keresztül:
Forgatás és húzás esetén a v vágási sebességet a gyalugép vágó sebessége határozza meg, és vágás közben húzza a munkadarabhoz képest.
Hegesztés és szupervízelés esetén a vágási sebességet az eszköz tengelyirányú elmozdulása (lásd az 1.4, e, g ábra) figyelembe vételével határozzák meg.
A vágási sebesség a legnagyobb hatást gyakorolja a folyamat termelékenységére, a szerszám tartósságára és a kezelt felület minőségére.
Az eszköz előtolási sebességét a sebesség sebessége határozza meg. Az esztergálás, fúrás, őrlés és őrlési rendszer paramétereinek technológiai számításaiban a munkadarab adagolásának koncepcióját így egy fordulatnál használjuk, és ez mm-ben kifejezve. A fordulatszámú fordulatszám számszerűen megegyezik a szerszám mozgatásával egy forradalom alatt:
Forgatáskor az előtolást a szerszám lökete határozza meg. Csiszoláskor az előtolás a szerszám löketével vagy kettős lökettel látható. A fogak adagolását a marás során a szerszám Z fogainak száma és a forrástérfogat alapján határozzák meg:
Az A vágás mélységét a munkadarab feldolgozott felületétől a munkadarabig, a normál értéktől függően, mm-ben határozzák meg. A vágás mélysége a szerszám minden egyes munkaüteméhez van beállítva. A hengeres felület megfordításakor a vágási mélység a z átmérők fél közötti különbsége: feldolgozás után:
ahol d a munkadarab kezelt felületének átmérője mm. A takarmány mérete és a vágási mélység határozza meg a folyamat termelékenységét, és nagy hatással vannak a kezelendő felület minőségére.
A folyamat paraméterei közé tartozik a vágószerszám geometriája, vágóereje, feldolgozási kapacitása és az eszköz élettartama.
A vágószerszám geometriai paramétereit a kések felületének metszéspontja, valamint a vágópengék felületének a megmunkált felülethez viszonyított helyzete és a fő mozgás iránya határozza meg. Ezek a paraméterek azonosak a különböző típusú eszközökhöz, ami lehetővé teszi számunkra, hogy az esztergáláshoz használt eszköz példáján keresztül vegyük figyelembe őket.
Az elülső és hátsó felületek mentén a vágószögeket bizonyos koordináta-síkon mérik. Az 1. ábrán. A 2.1a. Ábra a koordináta-síkokat mutatja az esztergálás során; 2.1, b a szerszám sarkai a statikában.
Fő elülső sarok # 947; - a penge elülső felülete és a vágás síkjára merőleges sík közötti szög; fő hátsó sarok # 945; - a penge hátsó felületének és a vágó síknak a szöge; élesítés szöge # 946; - Az elülső és a hátsó felület közötti szög. A szögek építésének elvéből következik
# 945; + # 946; + # 947; = π / 2.
Az X vágóél dőlési szöge a vágóél és a fő sík közötti vágási sík szöge.
Szögek tervben: a fő szög a tervben # 966; - a fő sík szöge a vágó sík pályája és a hosszirányú betáplálás iránya között; segédszög tervben # 966; ' - A fő sík szöge a segéd vágóél és a megmunkált felület között.
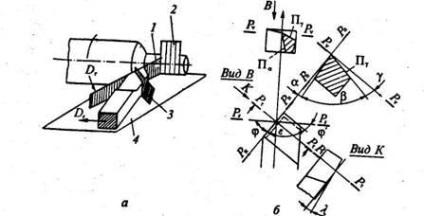
Ábra. 2.1. A forgószerszám geometriai paraméterei:
a - koordináta síkok; b - a szerszámszögek a statikában;
1 - Pn vágási sík; 2 - Ps munka sík; 3 - a Pt alapcsapágy síkja; 4 - a fő sík Pv
A vágószerszám geometriai paraméterei jelentősen befolyásolják a vágóerőt, a felületi minőséget és az eszköz kopását. Így, ahogy az y szöget megnöveli, a szerszám könnyebben behatol az anyagba, a vágóerők csökken, a felület minősége javul, de a szerszám kopása nő. A szög jelenléte csökkenti a szerszám súrlódását a vágófelületen, csökkenti annak kopását, de túlzott növekedése gyengíti a forgácsoló élét, és hozzájárul a rázkódás hatásához.
A P vágóerők a forgácsolószerszámra ható erők az elasztoplasztikus deformáció és a vágott forgácsok megsemmisítése során.
A vágóerők a penge csúcsához vagy a vágóél pontjához vezetnek, és az xyz négyszög koordinátarendszer koordinátatengelyei mentén ábrázolódnak (2.2. Ábra). Ebben a koordinátarendszerben a z tengely a fő mozgás sebessége mentén irányul és pozitív iránya megfelel a szerszámon megmunkálandó anyag irányának. Az y-tengely a csúcs fő mozgáskörének sugara mentén van irányítva. Pozitív iránya megegyezik a szerszámon a fém hatásának irányával. Az x tengely irányát a jobb koordinátarendszer kialakításának feltételei közül választjuk ki. A vágóerő értékét több tényező határozza meg. A vágási sebesség és az előtolási sebesség h növekedésével nő (a vágott forgácsok keresztmetszete), a vágási sebesség # 957; az első sarok leeresztése # 947; vágószerszámok. Ezért a forgácsoló erő kiszámítása az egyes kezelési módszerekhez kialakított empirikus képletek szerint történik (lásd a megmunkálási kézikönyveket). Például ennek a képletnek a tervezéséhez P = Cp h Xp s Y p X n, ahol a Cp. Chr. Yp. n jellemzi a munkadarab, a vágó és a feldolgozás típusát.
A vágási folyamat erejét a skaláris termék határozza meg:
Ezt a terméket a koordináta tengely mentén lévő vetületeken keresztül expresszálva kapjuk:
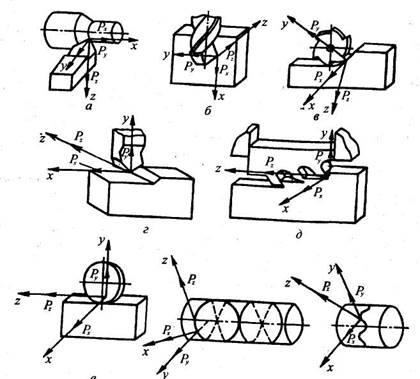
ahol vx. vy. vz - a keletkező vágóerők alkalmazásának sebessége koordináta-tengelyére vonatkozó kiugrások. Gyakorlati számításoknál a hozzávetõleges függõséget N = Pz v használjuk. Ez az egyszerűsítés annak a ténynek köszönhető, hogy a teljes forgácsolóerő Py és Px komponensei kicsiek a P2-rel szemben. és az adagolási sebesség a vágási sebességhez képest csak 0,1%.
Ábra. 2.2. A szerszám forgácsoló élén a forgácsolóerők hatásmechanizmusa egy olyan helyen, ahol a legnagyobb mozgási sebesség van # 957; feldolgozáskor: a - esztergálás; b - fúrás; in - marás; r - gyalulás; húzással; e - honing; g - szupervízelés.
A vágási feldolgozási kapacitást az egységnyi időegységben gyártott alkatrészek száma határozza meg: Q = \ / Tm. Egy gyártási idő Tm = Tg + Tm + Tkp. ahol To - a vágási folyamat által felhasznált megmunkálási idő meghatározása minden folyamatnál; Tt - a szerszám megközelítési és visszahúzási ideje egy részlet feldolgozása során; GVSp - kiegészítő telepítési idő és eszközbeállítások.
Így a megmunkálás termelékenységét elsősorban a T0 gépi idő határozza meg. Fordításkor min: To = La / (nso h), ahol L - a szerszám löketének becsült hossza, mm; a - a feldolgozásra jogosító támogatás nagysága, mm.
Az a / h arány jellemzi az előírt vágánymenetek számát az I. vágási mélység megmunkálásakor. Ezért a legnagyobb termelékenység a h = a vágási mélység, az s0 maximális előtolási sebesség és a maximális vágási sebesség megmunkálása esetén lesz. A termelékenység növekedésével azonban a felület minősége csökken és a szerszám kopása nő. Ezért a vágásnál a feladat a maximális megengedett kapacitás megteremtése, miközben fenntartja a kívánt felületi minőséget és a szerszám élettartamát.