Lime kemence
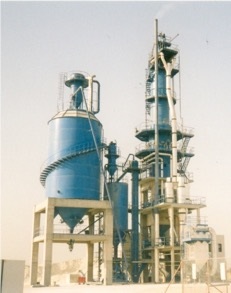
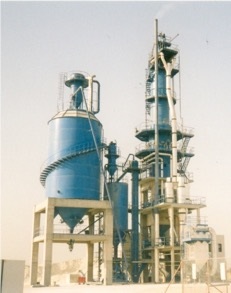
Az égetőműben az égéstermék előállításához a mészkő-kalcinálási eljárást (CaCO3) magas hőmérsékleten hajtják végre földgázként, tüzelőanyagként.
Hőhatás alatt a mészkő kalcium-oxidra (égetett égés) és széndioxidra (széndioxidra) bomlik:
CaCO3 + Hő ↔ CaO + CO2
100 gr. 56 g. 44 g.
Ezt a kémiai reakciót a következő tényezők befolyásolják:
- Bomlási hőmérséklet.
- A mészkő összetétele.
- A mészkő fizikai jellemzői (frakció).
- A kemence műszaki jellemzői.
A bomlási hõmérséklet
A bomlási hőmérséklet a szén-dioxid (CO2) részleges nyomásától függ.
Elméletileg, atmoszférában kipufogógáz (a atmoszférát alkalmazunk a kemencében), a negatív nyomás és a CO2 koncentráció a szén-dioxid 25%, az expanziós folyamat kezdődik hőmérsékleten 810 ° C, míg a 100% CO2 koncentráció folyamat kezdődik hőmérsékleten 900 ° C-on, például a a 2.1 ábrán látható.
A gyakorlatban túlságosan nagy mennyiségű hő szükséges a mészköves kő teljes bomlására, mivel a mészkő felületén képződött kalcium-oxid réteg hőszigetelő.
Ezért a mészkő felületét több mint 900 ° C-ra kell melegíteni, különösen akkor, ha az alacsony reakcióképességű mész keletkezik. Ehhez szükséges a kő felületének felmelegítése közel 1300 ° C-ra, a szikla részleges szinterezésével.
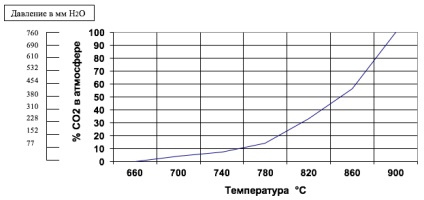
A reaktivitás ebben az esetben olyan időintervallumot és elegendő energiaellátást jelent, amely a hidratálási reakció teljes ciklusának végzését végzi az égető termelés során. Emiatt fontos tényező a fenti értékek ellenőrzése a sütés során.
A 2.2. Ábra azt mutatja be, hogy a kerek formájú mészkő kalcinálási ideje és a 1100 ° C állandó hőmérsékletű hőfogyasztás mennyiben korrelál. Az első órában kalcinálási hőigény lényegesen magasabb, akkor jelentősen csökken, mert a már létrejött a felületén egy kő a kalcium-oxid (CaO), a fent leírtak szerint, működik, mint egy hőszigetelő réteget.
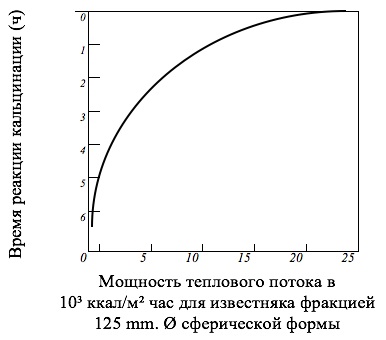
Az üregek százaléka nem változik, ha a kövek szabálytalan alakúak. A felület nagysága a frakció méretétől függ.
A gyakorlatban, a kvalitatív szitálási képződött üregek térfogatszázaléka kitöltésekor kemence szabálytalan alakú kövek elérheti a 50%, de amikor belül mozgó a kemencét és őrölt mészkő üregek százalékában elérheti akár 25%, amint azt a 2.3 ábra:
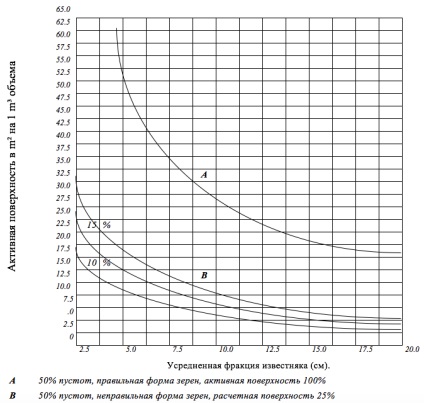
A grafikon jól mutatja, hogy minél nagyobb a felület, annál hatékonyabban működik a kemence.
Ezért figyelembe kell venni a mészkő tartózkodási idejét a kemencében és a hő abszorpcióját a kő mozgatásának folyamata során az előmelegítő zónából a tüzelési zónába. Ezzel elkerülhető a termék minőségének csökkentése és a felesleges hőenergia csökkentése.
A GALÉRIA KÉMIAI TULAJDONSÁGAI
A kalcitumból álló mészkő főleg kalcium-karbonátot (CaCO3) tartalmaz. Mivel a szennyezők általában jelen vannak: bizonyos mennyiségű magnézium-karbonát (MgCO3), szilícium-oxidok (SiO2), vas (Fe2O3), alumínium (Al2O3). A mészkő olyan stabil kőzet, amely nem változtatja meg szerkezetét 600 ° C-ig; magasabb hőmérsékleten vízben gyengén oldódik és szén-dioxidot bocsát ki.
A mészkő fő jellemzője, hogy képes magas hőmérsékleten lebomolni, miközben égető mázot képez, amelynek előállítása ipari méretben az egyetlen nyersanyag.
A GALÉRIA FIZIKAI JELLEMZŐI
A legfontosabb fizikai tulajdonsága a mészkő mérete és alakja van, amely meghatározza a terület a levegővel érintkező, ami viszont befolyásolja a hőkapacitása, hő behatolása sebessége belül a gabona, és végső soron a minőséget a kapott terméket.
Másrészt a szemcsék mérete és alakja meghatározó tényező a gázáramok eloszlásában a képződő üregek felett.
Ennek megfelelően minél kisebb a kő frakció, annál nagyobb a felület. Ez csökkenti a hő áthatolásának sebességét a kőbe és az aktív felületre (lásd az alábbi táblázatot).
Átmérő hüvelykben
Zeren a kockán. ft
A négyzet alakú gabona területe. hüvelyk
AZ EGYSÉGES FELÜLET CSOMAGBEN ÁLTALÁNOS JELLEMZŐI
A tervezési folyamatban olyan paraméterek, mint a kemencemagasság, keresztmetszet, bélés, rakodási zár, kirakodó mechanizmus, tüzelőanyag-ellátó és égetőrendszer, hőenergia alkalmazása stb. figyelembe véve a mészkő fizikai és kémiai szerkezetét. Különös figyelmet fordítanak erre, mivel a nyersanyagok tulajdonságainak vizsgálata garantálja a késztermék megfelelő minőségének és deklarált jellemzőinek megszerzését.
A CBK modellkemence négy fő szakaszra oszlik: (fentről lefelé):
- Letöltés szakasz
- Előmelegítési szakasz
- Kalcinálás vagy kalcinálás
- Hűtési szakasz
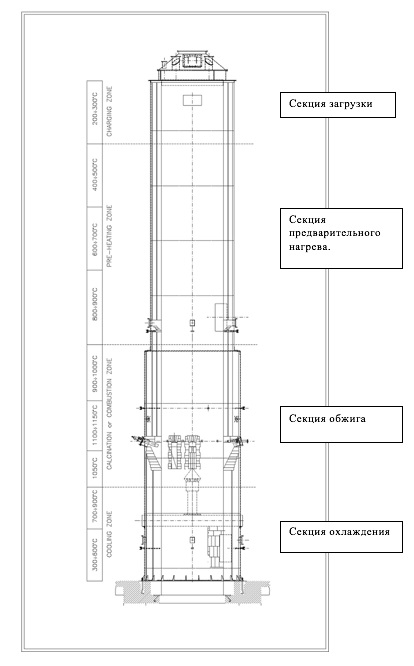
AZ ÉLELMISZEREK LEÍRÁSA
LETÖLTÉS SZEKCIÓ
A csomagtartó rész közvetlenül a terhelés zárak alatt található. Ebben a szakaszban a kemencébe bejutó mészkő a tengely mentén oszlik el és elsődleges ellenáramot vesz fel forró kipufogógázokkal (180-300 ° C).
Előmelegítő rész
Az előfűtő mészkő továbbra is felmelegszik forró kipufogógázok, de magasabb hőmérsékleten (900 ° C és 300 ° C alulról felfelé), és végül, miután a teljes átviteli szakasz hozzuk 800 ÷ 850 ° C hőmérsékleten.
TERÜLETI ZÓNA
900 ° C és 1150 ° C közötti hőmérsékleti környezetben a mészkő bomlása (CaCO3) bomlik kalcium-oxidra (CaO) és szén-dioxidra (CO2); A hőáramot hő sugárzás és konvekció biztosítja.
HŰTÉSI SZAKASZ
A hûtõszakasz szükséges ahhoz, hogy a keletkezõ meszet a tûztõhõmérséklet (1100 ° C) és a kibocsátási hõmérséklet között (<100°C) в процессе теплообмена с воздухом, который поступает с днища печи, проходит через слой горячей извести и в результате теплообмена нагревается до 900°C.