A forrasztásos paszták mindegyike a fő
Olyan pasztákkal, amelyek speciális folyadékokkal való mosást igényelnek, a helyzet más. Függetlenül attól, hogy a jelenléte halogének a készítményben, az ilyen paszták alapulnak fenyőgyanta fluxus, ezért a mosás után forrasztás használata ajánlott oldószer típusát és HCFC elszappanosított reagenst. Ezután a mosófolyadékokat desztillált vízzel, majd ionmentes vízzel mossuk.
Ugyanakkor sok halogén forrasztópasztát nehezen tisztítanak, és a fehériték fehérje maradványa a lemezek felületén marad. Ebben az esetben a vázlat ellenállása fontosabbnak tekinthető, mint a mosható.
A legtöbb forrasztópaszta, amely nem igényel mosást, szabadon termel ebből a folyamatból. Az ilyen paszták átáramlása védi a keményforrasztott ízületet a korróziótól, mint egy lakk. Fókuszáljon olyan mosogatószeres pasztákra, amelyek a legtechnológiailag legfejlettebbek.
Ábra. 2. Forrasztópaszták összetétele
Gyakran mondják: a nem mosó paszta nem tartalmazhat halogéneket. Világosan meg kell érteni, hogy ha a dokumentációt a massza a „meg kell tisztítani”, hogy kell mosni, és ha az ilyen címkézés nem, akkor a probléma megoldódik alapján további követelményeket a termék: a megjelenés, lakk.
Japánban például halogénezett paszták (0,2%) a forrasztás utáni mosás nélküli eljárások sokkal népszerűbbek, mint a halogénmentesek. Halogén-tartalmú forrasztópaszták viszonylag gyárthatóak, mint például a forraszthatóság, de gyakran halogénmentes tészták rosszabb megbízhatóság, így csökken a szigetelési ellenállás a kész szerelhető. Ez a fluxusmaradványok magasabb kémiai aktivitásának tulajdonítható. Így a forraszthatóság és a megbízhatóság a legtöbb esetben kölcsönösen kizáró tényezők.
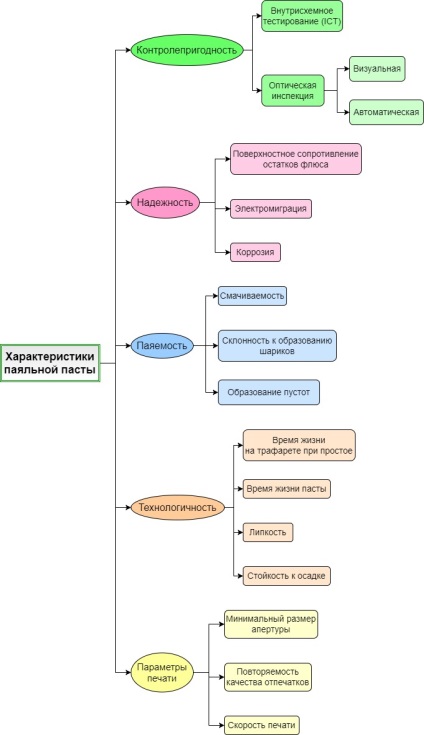
Ábra. 3. A forrasztópaszták kifejlesztésében vagy kiválasztásában figyelembe vett fő jellemzők
Ideális esetben a mosás nélküli forrasztáshoz halogén nélküli pasztára van szükség, de forraszthatósággal, mint halogéntartalmú paszta.
A nehézség a halogénmentes paszta paszták kémiai aktivitásának növelése. A legtöbb ilyen pasztában szerves savakat használnak aktivátorként a halogéntartalmú vegyületek helyett, annál kisebb a molekulatömeg a savban, annál nagyobb az aktiválási kapacitás. Mivel a szerves savak aktiváló hatása sokkal gyengébb, mint a halogéntartalmú komponenseké, néhány tíz viszonylag aktív szerves savval próbálják bevezetni a fluxus rendszerét.
Ugyanakkor ilyen erősen aktív szerves savak felszívják a nedvességet. Ez tele van: a szubsztrátum felületén lévő fluxusmaradékokban maradt savak ionosak, ha kölcsönhatásba lépnek a vízzel, ami csökkenti a felületi szigetelési ellenállást és elektromigrációhoz vezet.
Íme néhány példa a népszerű pasztákatípusokra:
- forrasztópaszta nagy sebességű nyomtatáshoz;
- forrasztópaszta magas nedvesítő képességgel;
- forrasztópaszta automatikus áramköri teszteléshez;
- Univerzális paszta rendkívül hosszú élettartammal a sablonon.
2. táblázat A forrasztópaszta életciklusa a termelésben
A paszta életciklusának szakaszai
Kívánatos, hogy a nyílás mérete valamivel kisebb legyen, mint a PCB-ben található pad, hogy kompenzálja a képernyő nyújthatóságát, az illesztési tűréseket és a forrasztópaszta vájatát. A 9. ábrán a ház QFP kimenetének érintkezési felületén (0,5 mm-es szög) lévő nyílás példája látható.
Ábra. 9. A sablonban lévő lyuk méretének kisebbnek kell lennie, mint a helyszín méretének
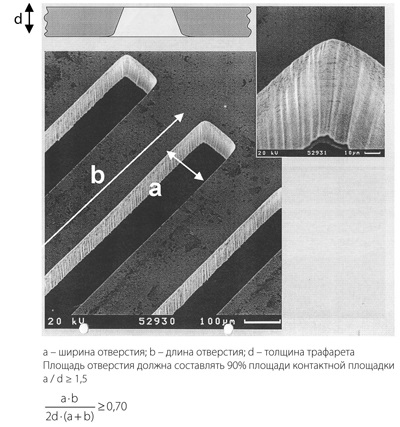
Ábra. 10. A lyuk méretének kiszámítása a sablonban
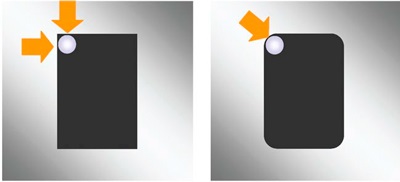
Ábra. 11. A lekerekített sarkokban lévő lyukaknál a paszta és a lyukak falai közötti tapadás kisebb
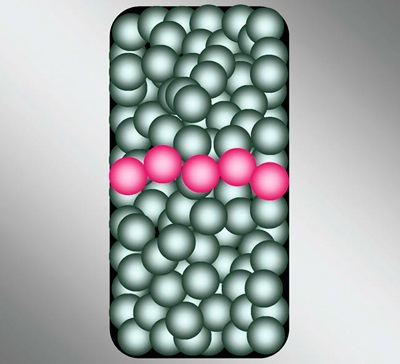
Ábra. 12. A legkisebb nyílásnál a sablonnak a legnagyobb forrongó golyók közül 4-5-nek kell illeszkednie
A nyílások geometriai alakja erősen befolyásolja a forraszavarok számát. Ezért a sablonok gyártásának nagyon felelősségteljesnek kell lennie mind a tervezési, mind a gyártási szakaszban.
Kiszámítására vonatkozó szabályok méretek a nyílások a 10. ábrán szemléltetjük a 11. ábra azt mutatja, hogy amikor a nyílások, lekerekített sarkokkal csökkenti a tapadást a paszta és a falak, a nyílással, amikor a sablon a szubsztrát rekesz, amely csökkenti torzítása az ujjlenyomat.
Ami a legkisebb rekesz méretét illeti, a legnagyobb forrasztóbolyók közül legalább ötnek a legkisebb nyíláson kell elhelyezkednie a kisebb oldalon (lásd a 12. ábrát).
A Rakeli gumi és fém. A gumibetétek négyzet alakúak, laposak és szablyának vannak osztva (lásd a 13. ábrát). Nem tudjuk megmondani, hogy melyik a gumibetét a jobb: a munka a lehúzási szög függ kiegyenlítő pépek, és jó folyási ad tiszteletére töltő minden nyílás a forrasztó paszta.
Az ütőszerszám munkasíkja 70-80 °. Mivel a lefelé irányított erő viszonylag kicsi, az ilyen gumibetét alkalmasabb az alacsony viszkozitású paszták számára.
Egy gumiszalaggal a munkaszög 45 °. Nagy nyomást gyakorol a forrasztópaszára, ezért jobb használni a nagy viszkozitású pasztákhoz. Ha alacsony viszkozitású pasztával viszi ezt a gumibetétet, a paszta a sablon alatt foltlik (lásd a 14. ábrát).
A lapos szerszám munkasíkja 50-60 °. A dőlésszög megváltoztatásával különböző viszkozitású pasztákkal dolgozhat.
Gumiszalaggal való munkavégzés során folyamatosan ellenőriznie kell, hogy a munkaéle mindig éles-e. Ha a szél elhasználódott, növelje a nyomást, hogy elkerülje a paszta elkenését. Ez megnöveli azt a nyomást, amely alatt a nyílások betöltik a pasztát, ami növeli a forraszanyag részecskéinek súrlódását és hátrányosan befolyásolja a paszta elválaszthatóságát a nyílások falától.
A gumiból eltérően a merev fém pengék nem kopnak ki, hosszú ideig dolgoznak, és nem ragadják meg a paszta a lyukakat.
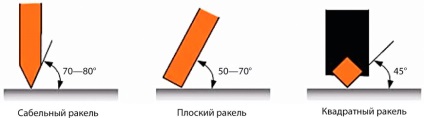
Ábra. 13. Gumitömlő típusok
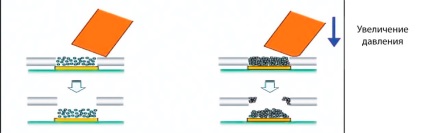
Ábra. 14. Fagyasztott paszta a sablon alatt, ha a párna / paszta viszkozitás párja helytelenül van kiválasztva