Anyagtudomány laboratóriumi gyakorlat
GU VPO „belorusz-orosz Egyetem”
Összeállította: Dr. Sc. Sciences, prof. FG Lovshenko
cand. tehn. Sciences, Assoc. GF Lovshenko
Art. tanár AI Habibullin
Véleményező tudomány kandidátusa, egyetemi NS NS Garlachov
Az elméleti alapok és irányelvek végrehajtása a következő laboratóriumi munka Exchange „Anyagok”: „kémiai-hőkezelése acél”, „szines fémek és ötvözetek”, „Válogatás acél és hőkezelés hozzárendelés mód.”
Felelős a megjelenése GF Lovshenko
Írásszedő NP Polevnichaya
Aláírták a nyomtatott formátum 60x84 1/16. Ofszet papír. Headset Times.
Sablonos sokszorosítás .Usl. Pec. l. Jaj. -izd. l. Circulation 215 példányban. rendelési szám
Kiadó és nyomtatása:
Az állam felsőoktatási intézmény
15 Lab № 15. kémiai-hőkezelése acélból
A cél a munkát. megismerése az általános rendelkezések termokémiai kezelése elmélet; tanulási folyamatok kritikus-termokémiai kezelés és a rétegek a szerkezet acél után XTO.
Termokémiai kezelés (HTO) nevezett technológiai folyamatok vezető telítettség a diffúziós felületi réteg részek különböző elemeit. HTO használják, hogy növeljék a keménység, kopásállóság, fáradtság ellenállás és a kapcsolattartó fáradtságot, és számára is védelmet elektrokémiai korrózió és a gáz. Az XTO tétel környezetbe helyezzük gazdag telítő elem. Az XTO előfordulhat három alapvető folyamatok: disszociáció, felszívódás és a diffúzió. A disszociációs fordul elő egy gáznemű közegben, és tartalmaz egy szétesését molekulák és kialakulásának aktív atomok diffúziós elemet. A disszociációs mértéke a gázmolekulák nevezzük disszociációs mértéke. Felszívódás történik a „fém-gáz” és az, hogy felszívja a fém felületén telítő elem. Kevesebb diffúziós észre mély behatolás elem telítődő fém. Ennek eredményeként, a diffúziós réteg képződik HTO.
A legmagasabb koncentráció a telítődő elem figyelhető meg a cikk felületén, mint a távolság a felület csökken. Fázis és strukturális változások előforduló XTO a diffúziós réteg, és annak szerkezetét határozza meg izoterm metszeti fázisdiagramja a „kezelt fém - telítőanyagot elemek” alatt diffúziós telítési hőmérséklet.
Tegyük fel, hogy a rendszer „A kezelt fém - telítési elem B” megfelel az állapotdiagram ábrán látható 15.1. és a telítettség történik t1. Amennyiben a disszociáció folyamatok, felszívódás és a diffúziós folytassa aktívan és telítési idő elég, akkor képződik a felületi réteg egy szilárd oldat és változó koncentrációjú. réteg lesz a szilárd oldatban és az alatta és B egy kémiai vegyület az An és Bm változó koncentrációjú több szilárd oldat B és A, csökkentésével a telítési határérték nullára. A határok között, a rétegek koncentrációja változik szakaszosan ábra szerint a rendszer állapotát. Eloszlás telítési elem a diffúziós réteg vastagsága, és a szerkezetét mutatja be 15.2 ábra.
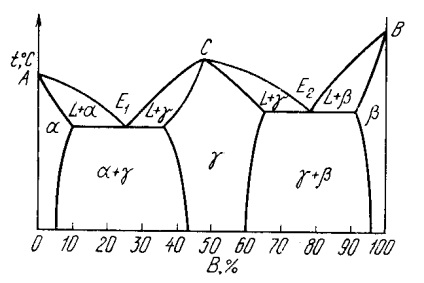
15.1 ábra - A fázisdiagram az ötvözetek korlátozott oldhatósága és kémiai vegyület
15.2 ábra - koncentráció változását a diffundáló szerinti elem a rétegvastagság
Két-fázisú régió a diffúziós réteg nem képződik a XTO folyamatban. Azonban, ezek a területek jelennek során lassú hűtés a diffúziós telítési hőmérsékletű ötvözetek alávetni másodlagos kristályosodás.
A leggyakoribb típusú kémiai-termikus kezelés carburizing, nitridálás, cyaniding (karbonitridálás), boriding, króm.
0,3%. Cementálás melegítéssel végezzük, és lassú zár részeit egy carburizing atmoszférában hőmérsékleten ausztenites állapotban az acél. karburizálás hőmérséklete 900-950 ° C carburizing leggyakrabban elvégzett gázatmoszférában vagy egy szilárd karburéval. A gáz karburizálás kialakulását atomi szén fordul elő disszociációja következtében telített szénhidrogének
Amikor carburizing szilárd karburéval atomi szén által alkotott disszociációs szén-monoxid
Szénsav BaCO3 sót. Na 2CO 3. K2 CO3. adunk a szén mennyisége 10-30%, aktivátorai, amelyek felgyorsítják a kialakulását szén-monoxid
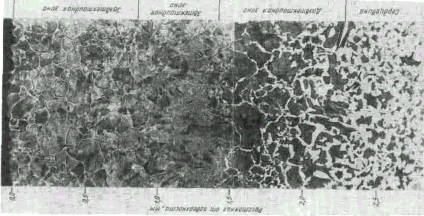
Ábra 15.3 - a mikroszerkezete felületi tartományában az acél alá carburizing
Azotirovaniemnazyvaetsya felszíni telítési folyamat elkezdődött nitrogénnel. Arra használják, hogy javítsa a keménység, kopásállóság és a fáradtság limit és a korrózióállóság gépalkatrészek. a nitridálási folyamatot hajtjuk végre 480-650 ° C-on 30-90 órán át atmoszférában ammóniagáz, disszociáló reakciójával
A kapott atomi nitrogént adszorbeálva a felületre, és bediffundál a fém.
Változások a mikroszerkezete felületi zóna (ábra 15.4, b) előforduló a nitridálási kezelés képviselt alapján a diagram „vas-nitrogén” (ábra 15.4, a). Ebben a rendszerben, a kialakulását a következő szakaszokból áll: - nitrogén ferrit; - nitrogén ausztenit; - nitrid FE4 N; - nitrid Fe3 N. Sok ötvözőelemek nitrogén és képez egy kémiai vegyületet - nitridek (CrN, CR2 N, MNn, TiN, MoN, AIN, stb).
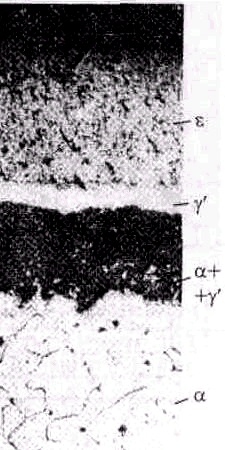
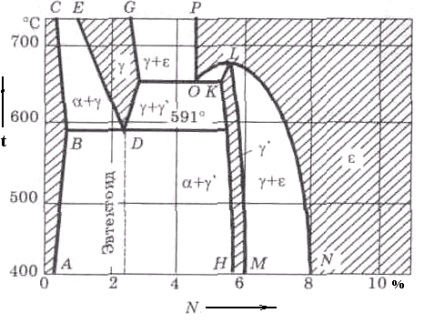
Ábra 15.4 - Fe-N rendszer diagram (a) és a felület régió mikroszerkezetének acél vetjük alá nitridálás (b)
Ezzel ellentétben a vas, a szén jelenléte az az acél kialakulásához vezet a felszínen a diffúziós réteg karbonitridek fázis típusú Fe3 (C, N) vagy Fe3 (N, C).
Amikor nitridálhatunk ötvözött acélok együtt a fenti fázisok - , , , , szimultán alakítjuk nitridek ötvözőelemek. Hogy növelje a keménység és tartósság a folyamat nitridáiási acél van kitéve egy speciális, úgynevezett nitralloi. Ezek tartalmazzák az alumínium, króm, molibdén, amely stabil ellen koagulációs és a növekedés a nitridek. Leggyakrabban kitéve nitridáláshoz acél 35HMYUA, 38HMYUA, 38H2MJuA, 35HMA. A nitrálást úgy hajtjuk végre 500-520 ° C-on A hordozót -keménység zónában. A hűtés során nitralloev a nitridálási hőmérsékleten a szobában, annak következtében, oldhatóságának csökkentése ötvözőelem -zóna alakul nagyon diszperz spetsnitridov CrN, MoN, AIN. Ezek a diszpergált részecskék akadályozzák a mozgást diszlokációk, és ezáltal növelik a keménysége a nitridkéreg.
A keménység a hagyományos szerkezeti acélok után nitridálási viszonylag alacsony. Ebben az esetben, a különleges vas nitridek panel ellen koagulációs csak alatti hőmérsékleten 450 ° C-on
Ahhoz, hogy javítsa a fáradtság erőt a hagyományos építési nitridált króm-nikkel acél.
Annak érdekében, hogy a korrózióállóság javítása vethetjük alá semmilyen nitridálás acél. Az eljárást hajtjuk végre 600-700 ° C-on 0,5-1,0 órán keresztül. Korrózió ellenállás megnövekedett képződése következtében a felület szilárd termék -fázisban.
Nitridáláskor a végső feldolgozás. Hőkezelés - javulás álló edzett és megeresztett megelőzi Nitridált.
Alávetni nitridáláshoz ilyen részleteket, mint a bélés hengerek, főtengelyek és a dízelmotorok, tengelyek, orsók, ólom csavarokat és csőszerű termékek szerszámgépek, fogaskerekek.
Tsianirovaniemnazyvaetsya egyidejű telítettségét szén és nitrogén felületi részletek. Megkülönböztetése magas és alacsony hőmérsékletű lehasítsuk.
Nagy-cianidos végezzük 800-950 ° C-on a felhasználás célja szerint növekedés keménység, kopásállóság és a fáradtság erőt gépalkatrészek alacsony széntartalmú és közepes rendes és ötvözött acélok. Miután ciánozózónábói magas és alacsony edzés kell hagyni.
Alacsony hőmérsékletű cianidos hajtjuk végre 540-580 ° C-on és főleg, hogy fokozza a stabilitást a végső hőkezelt nagy sebességű acél eszközök.
cianidos eljárást hajtjuk végre folyékony és gáznemű közegekben. Folyékony cianidos végezzük a fürdő keverékében olvadt sók típusú cianid NaCN, KCN, Ca (CN) 2 típusú semleges sók NaCl, Na 2CO 3. BaCl2. BaCO3. A hátrányok a folyamat a nagy folyadék cianidos mérgező cianid sók és a magas költségek.
Gáz nazyvayutnitrotsementatsiey cianidos. Ezt a folyamatot végezzük elegyében nitridképző gáz és carburizing. Mivel karburizálás lehet bármilyen gáz során alkalmazott gáz carburizing - természetes pirolízis, keveréke a földgáz és a gáz - hígítószer. Nitridálási gáz ammónia. gáz arány: 5-30% 95-70% ammónia és carburizing gáz.
Jelenleg, a magas hőmérsékletű gáz cianidos (karbonitridálás) széles körben bevezetett helyett gáz carburizing. Magas hőmérséklet cianidos végezzük alacsonyabb hőmérsékleten, mint a gáz carburizing. Emellett tsianirovannye termékek keménység és kopásállóság kiváló cementált. Ez annak köszönhető, hogy a jelenléte diffúziós réteg nemcsak a szén, de a nitrogén.
Borirovanie- ez a diffúziós telítettségét a felületi réteg bór. Az eljárást úgy hajtjuk végre, hogy javítsa a felületi keménység és kopásállóság, és a korrózióállóság. A legígéretesebb ipari felhasználásra a porkeverékek boriding olvadt sók és oxidok paszta (bevonat), és a gáz boriding.
A szilárd borozást bór-karbiddal (B4C) vagy bór-oxidon (B2O3) és alumíniumon alapuló fém-termikus elegyeken alapuló porkeverékekben végezzük. A telítési folyamat aktiválásához NaF vagy NH4Cl sókat adunk a keverékhez 0,5-3,0% mennyiségben.
Borítás a bevonatokból ajánlatos alkalmazni, ha szükséges a nagyméretű termékek megkötése vagy az egyes részegységek helyi borálásához. A borok szállítói bevonattal telítettek, amorf bór, bórkarbid vagy bór-oxid. A kezelt termék felületén a bevonatokat ecsettel alkalmazzuk. A leggyakrabban használt bevonatok, amelyek két rétegből állnak - aktív és védő. A védőréteg oxigéntartalmú atmoszférában védi az aktív anyagot a borítási folyamat során az oxidációtól.
A sók és oxidok olvadása az elektrolízisre és elektrolízisre oszlik. Az elektrolízis bórízesítését a borax (Na2B4O7) olvadékában végezzük. Az eljárást 0,08-0,25 A / cm 2 állandó áramsűrűség mellett végezzük.
A munkadarab katód. A bórmentesítést bór-tartalmú anyagok (B, B4C, stb.) És semleges sók olvadásával végezzük.
A gázboronizációt a gáznemű bórvegyületek bomlásával kapott közegben végezzük. A leggyakrabban használt diborán (B2H6) és bór-triklorid (BCl3), amelyeket hígítanak gázokkal, amelyek nem tartalmaznak bórt (H2, Ar, N2).
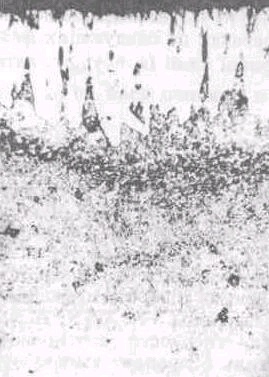
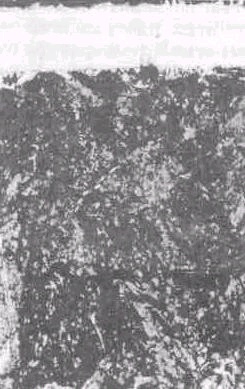
15.5 ábra - A bór (a) és a krómozás alá eső acél felületének mikrostruktúrája (b)
A boridok zónája alatt egy átmeneti zóna van, amely szerkezetileg különbözik a magtól. A bór szilárd oldata, valamint a vasban lévő szén- és ötvözőelemek. Az átmeneti zóna vastagságát a bór behatolási mélysége határozza meg. A dopping elemek csökkentik az átmeneti zóna vastagságát.
A fúrás után a közepes, erősen terhelt alkatrészek keményedés és edzés hatásának vannak kitéve.
A borátort a gépek, szerszámok és szerszámok különböző részeinek megkötésére használják, amelyek intenzív kopás esetén működnek.
A krómot porkeverékekben, gáz- és folyékony közegekben végzik. A króm porkeverék krómszállítóból áll, amely krómporokat, ferrokromot, króm-oxidokat és olyan anyagokat tartalmaz, amelyek megakadályozzák a krómtartalmú részecskék szinterezését és a termékek felületének tapadását. Ezenkívül a sót hozzáadjuk a keverékhez, aktiválva a krómot. Nh4Cl, NH4Br, NH4J, NH4F aktivátorokat használnak.A krómtartalmú krómtartalmú aktivátorok kölcsönhatásba lépnek a krómtartalmú anyagokkal krómhalogenidek előállítására, amelyek az aktív króm atomok forrásaként szolgálnak.
Ha gázhalmazállapotú kromatográfiát alkalmazunk gázhalmazállapotú közegben, valamint porkeverékekben való telítettség esetén, az aktív króm atomok forrásai gázhalmazállapotú krómhalogenidek.
A krómtartalmú króm-klorid-sók (CrCl2 és CrCl3) olvadáspontja, valamint stabilizáló sója, amelyet a következő BaCl2 vegyületek egyikeként használunk. CaCl2. MgCl2.
A diffúziós konverziót krómnal 900-1200 ° C-on 4-10 órán keresztül végezzük.
A krómozás után a közepes és nagy terhelésű részeket később megszilárdítják. A krómozás növeli a szerszámgép élettartamát, alumíniumötvözetek öntőformát, különböző motorrészeket és magas hőmérsékletű gázturbinákat, olajszűrőket, szivattyúalkatrészeket és turbódrillákat, kötőelemeket.
Állásajánlás
1 Tanulmányozza a vegyi-termikus kezelés elmélete és technológiája.
2 Végezzen mikroanalízist a kémiai-hőkezelésnek alávetett minták gyűjteményének részeiben. Határozzuk meg és rögzítsük a diffúziós rétegek és a mag mikrostruktúráját (a vas-cementit és a vas-nitrogén állapot diagramjaival összefüggésben magyarázható acél és technikai vas mikrostruktúrája cementezéssel és nitridálással).
3 Grafikailag ábrázolják a kémiai-termikus és hőkezelési sémákat, magyarázzák meg azokat, jelezve a végrehajtott kezelési módok célját.
4 Mutassa be a vegyi-termikus kezelés megfelelő típusainak célszerű felhasználását.
5 Adja meg az adott típusú kémiai-hőkezelésnek alávetett acélok minőségét.