Hullámforrasztó - alapvető folyamat lépéseit
Jelenleg hullámforrasztó alkalmazzák forrasztóanyagként mellékletek és SMD alkatrészeket. Forr folyamat egyszerű. Kártyák telepítve a szállítószalag vannak kitéve fluxusállítás és előmelegítő, amely kizárja a hőguta szakaszában forrasztás. Ezután a lemezt áthalad a forrasztó hullám. A hullám maga a forma és a dinamikus teljesítmény a legfontosabb paraméterek a berendezés forrasztás. A hullámforma a fúvóka lehet változtatni; A korábbi tervek berendezések forrasztó szimmetrikus hullám. Jelenleg minden gyártó használja a saját hullám formájában (formájában a görög betű „omega”, Z-alakú, T-alakú, stb.) Irányát és sebességét a forrasztási folyást eléri a tábla is változhat, de meg kell egyeznie a teljes szélességét a hullám. A dőlésszöge a szállítószalag is beállítjuk táblák. Egyes berendezések forrasztó deshuntiruyuschim felszerelt légi kést, amely összegének csökkentését forraszanyag jumper. A kés található, közvetlenül mögötte a forraszanyag hullám és a múló lép működésbe, amikor a forrasztó még olvadt állapotban az áramköri lapon. A keskeny áramlás fűtött levegő, nagy sebességgel mozgó, hordozza azt a felesleges forraszanyag, így tönkreteszi a szövedékek és eltávolításának megkönnyítésére a forraszanyag maradékok.
Hullámforrasztó technológiával lehet osztani a következő műveleteket:
- fluxusállítás, eltávolítja a felesleges fluxus;
- előmelegítő;
- forrasztó;
- hűtés.
Az általános követelmények az osztályozás és vizsgálati módszerek a modern folyékony folyasztószerek vannak megadva a standard IPC / ANSI-J-STD-004, „követelmények forrasztás folyósítószerek”.
Folyósítószerek szokásosan két módja van:
- hab folyósító
- permet
A felhordási módszer fluxus hab folyósítószert csöves szűrőket alkalmazunk, amelyek alkotnak finom buborékos habot, javított nedvesítő-, különösen akkor, ha az átmenő borítás.
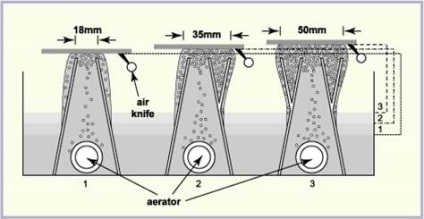
Az előnye ennek a módszer alkalmazása a folyasztószer - olcsó berendezés és az egyszerű beállítás fluxusállítás folyamat. Közül a hiányosságokat lehet hangsúlyozni - nagy fluxus fogyasztás és annak szükségességét, hogy kell üríteni, és alaposan mossuk fluxus habzó kő után forrasztás ciklusban.
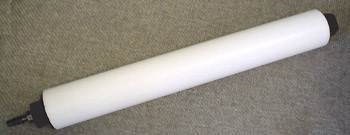
Csöves szűrőket, hogy egy finom buborék hab
Az optimális pórusméret kő 3-10 mikron. Telepítése előtt a kő kell oldószerben mossuk.
Folyósítószerek optimális feltételeket lehet elérni, ha a hab magassága kevesebb mint 2 cm.
Amikor a hab folyósító törölni kell szivárgó, fröccsenő, fúj ki (levegő kést) fluxus a felső oldalán az áramköri lapot a szélén csatlakozó.
Ahhoz, hogy eltávolítsuk a felesleges fluxus a felületről az áramköri lapot a hab folyósító
akkor ajánlott használni levegő kést.
Ez az eszköz csökkenti a folyasztószer maradékok a forrasztás után, és csökkenti szennyeződése az előmelegítő zónában.
Ez egy csövet fúrt lyukak ugyanazon a vonalon, ahol a levegő nyomás alatt van bejuttatva. Air késkészlet szállítószalag alá, merőlegesen az utóbbi.
Ajánlott légi kés dőlésszöge 10 ° között a lemez síkjára, és a gép a levegőben kés áramlását. levegő áramlási irányát késsel kell irányával szemben tábla mozgás. A távolság a levegő kést és folyósítószert zóna legyen legalább 10 cm annak érdekében, hogy megakadályozzák a fluxus habosítószerekkel.
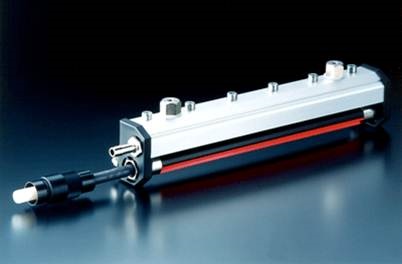
Az ajánlott távolság az áramköri kártya és a levegő kést -. 5 cm-es levegő nyomását úgy választjuk meg, hogy biztosítsa eltávolítása felesleges fluxus. Ebben az esetben, a forrasztószer nem szabad kitenni a felső oldalán a PCB, a élcsatlakozók. A levegő a szintén nem kéne fújni a habot flyusovatelya.
Folyósítószerek permet által összekapcsolt fúvókákkal, hogy a mozgás (egyidejű permetezés fluxus) felé elektronikus modul, mozgó a szállítószalag mentén.

Spray folyósító eljárás előnyös több okból is:
1. megszüntetése fluxus szennyeződés oxidok és egyéb szennyezőanyagokat kimossuk az a PCB felületéhez.
2. Pontos vastagságának szabályozása a fluxus, bevonat egy nyomtatott áramköri lemez (1-től 2 mikron).
3. mennyiségének csökkentése salakmaradványait a táblára a forrasztás után.
4. létrehozása technológiai előfeltételek az átmenet bezotmyvochnuyu technológia.
5. fogyasztásának csökkentése fluxus.
6. A szinte teljes kizárását a levegővel való érintkezés fluxus, növelve annak élettartamát.
7. csökkentése az oldószer elpárologtatása.
8. Csökkentett szennyeződés zóna folyósító és előmelegítő.
A hátránya ennek a módszernek, a magas költségek berendezések.
Amikor a porlasztásos folyósítószer kell behatolását megelőzzük fluxus a felső oldalon az áramköri kártyát a szélén csatlakozó.
2. Melegítsük elő a fedélzeten
A cél az előmelegítés, hogy előkészítse a nyomtatott áramköri lap érintkezik a forrasztó hullám, és csökkenti a hő-sokk.
Egy másik nem kevésbé fontos folyamat - az az oldószer eltávolítása. Hiányos Az oldószer elpárologtatása vezet válogatás nélküli kialakulását forraszanyag golyó hatására nyomtatott áramköri kártya és a forraszanyag hullám.
Így előmelegítés szükséges:
• fűtés a nyomtatott áramköri elektronikus alkatrészek csökkentése hősokk;
• Az oldószer eltávolítása a fluxus;
• aktiválása fluxus.
Válogatás előmelegítési hőmérséklet NYÁK tervezés,
oldószer párolgási hőmérséklet.
Melegítők használt előmelegítő:
infravörös IR, konvekció, kvarc.
Az alkohol-alapú folyósítószerek hagyományos mód, az alábbiak szerint:
Amikor vizes alapú fluxus növelésére van szükség a előmelegítési hőmérséklet 130-140 ° C (PCB) a teljes víz elpárolgását (nincs fő túlbuzgó, és figyelembe veszik a hőmérsékletet, amely tartjuk komponensek szerelve a táblán).
Amikor dolgozik egy többrétegű nyomtatott áramköri lapok különös figyelmet kell fordítani az alapos bemelegítés, ami minőségének biztosítása érdekében a forrasztási átmenő bevonatú lyukak.
A hőmérséklet-változás egy előmelegítési lépés kell végezni, amelynek mértéke nem haladja meg a 2 ° C / s.
Nem kielégítő fűtési és részleges az oldószer eltávolítása a forrasztás fluxus történik elgázosításra a forraszanyag hullám, ez rontja a nedvesítés és vezethet következtetéseket nepropayam komponenseket.
hőmérséklete a forrasz a forrasztási területen lehet beállítani a tartományban 235-260 ° C-on Minél alacsonyabb a keményforrasztási hőmérséklet, hogy csökkentsék a termikus sokk, hogy az elektronikus alkatrészek és a nyomtatott áramköri lemez, az oxidációs a forrasz, de növekedése miatt a felületi feszültség képes adni okot nepropaev, csatlakozók, forraszanyag tüskék. Magasabb hőmérsékleten, egészen 260 ° C-on általában beállítva a forrasztási többrétegű nyomtatott áramköri lapok. Annak érdekében, hogy jó minőségű forrasztott kötések szükséges, hogy a teljes forrasztás időszak tartományban 2,5-4 másodperc. Az érintkezési idő a forrasztott is függ a keményforrasztás hőmérséklete. Például, általában egy 250 ° C-on eléggé 2,5 sec, és a 235 ° C-on, miközben forrasztás kell növelni, hogy 3,5 mp. A tényleges hőmérséklet a PCB felületén mérhető keresztül a hőmérséklet-mérőkészülék profil, például, Érzékelő transzfer.
Beállításához a forraszanyag magassága hullám használata ajánlott hőálló üveg teszt táblák milliméter skála. Egyrétegű tábla optimális forrasztási hullám magassága kell terjednie 1/3 PCB vastagsága.
Tájékoztató értékeinek a merülési mélysége a PCB a forraszanyag hullám látható az alábbi táblázatban: