A projekt előkészítése az automatikus összeszerelési a nyomtatott áramköri lapok
Sok szempontból a minőségi SMT-egység rendelkezik a tervezési szakaszban a nyomtatási egységet. Annak érdekében, hogy csökkentsék annak valószínűségét, a beszerelés során problémát, valamint a költségek csökkentése, szükséges, hogy figyelembe véve a követelményeket a vállalkozás, a szerelő. Compliance biztosítja a legteljesebb végrehajtását az előnyöket, amelyeket magában felületszerelt technológiával.
Ezért figyelni, hogy a fejlesztési kérdéseket, amelyek közvetlenül befolyásolják a folyamatot, és a minősége a telepítést. Néhány az itt közölt információk általános jellegűek, és alkalmazható bármely termelés. Ezek alapján az ajánlások és szabványügyi szervezetek, az IPC (Institute for egymásba és csomagolás Elektronikus áramkörök) és JEDEC (Joint Electronic Device Engineering Council). Egyéb információ megszerzésének szakembereink alapján saját tapasztalatainkat berendezés. Mindenesetre, a gyakorlati alkalmazása a nyújtott információk segítenek, hogy felmászik a termék hatékony, gyorsan és hatékonyan.
beültetési
A berendezés az alkatrészeket minimális távolságra egymástól 0,2 mm, és a szélén a tábla - 1 mm (feltéve, hogy a technológiai területeken a munkadarab). De a használata a maximális műszaki kapacitását nem mindig indokolt. Ebben az esetben túl közel elhelyezése a komponensek nagyban csökkenti a karbantarthatóság a termék, optikai ellenőrzés a komponensek forrasztott kötések. A közelsége a komponensek különböző méretű és fajhő befolyásolhatja a minőségi forrasztás.
Ezen kívül fontos, hogy figyelembe kell venni, hogy a méretei ház sokkomponenses méreten túl a érintkező felületeket, így grafikák létrehozásakor alkatrészek kívánatos készíteni a tényleges méretek vagy által elfoglalt terület a komponens, figyelembe véve a szükséges helyet ellenőrzés és javítás. Ez segít kijavítani elemeinek elhelyezésére, és hogy elkerüljék a hibákat.
Ajánlott távolságok - 0,6 ... 0,8 mm közötti chip alkatrészek; 1 mm - között a chip komponens és a nagy tábla elemek 1,2 ... 1,5 mm közötti - a chipek és a főbb komponenseket, és 1,5 mm-es és keltetőkbe SMD alkatrészek (ld. 1.).
Orientációja komponensek nem számít, mert cégünk forrasztani hullámforrasztáshoz módszer nem alkalmazható.
Egyes fejlesztők ne habozzon rohanás van SMD-alkatrészek mindkét oldalán a PCB. Ebben az esetben a cikket kétszer halad szerelési lépést gépek írt program kétszer fordul elő kétszer a utánállításukra készült két stencil stb Érdemes csinál, ha a méret a fórumon is, mindenféle korlátozás a rések között a vezetékek, párna és egyéb elemek a tábla és egyéb követelmények nem hagynak választást. Ne feledje, hogy minden oldalon a fórumon kiszámítása a beszerelés költségét egy terméket. Emellett jelentősen növeli a költségeket a vizsgáló berendezés a vizsgálati nyomtatott áramköri lapok.
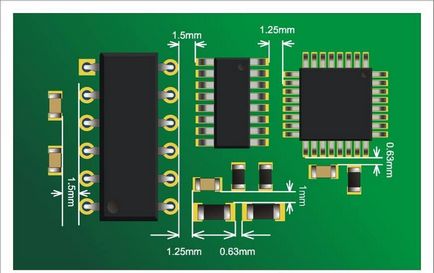
Abban az esetben, ha az egyoldalú elhelyezése a komponensek nem ajánlott kicsi, például a passzív elemek vannak elhelyezve az egyik oldalon a tábla és a chips és más „nehéz” komponensek - a másik oldalon.
Az alábbi ábra a besorolás szerint helyezzen tárgyakat az IPC PCB oldalon.
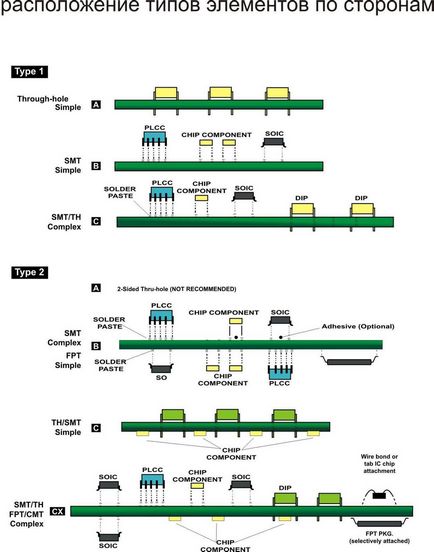
Párna.
Annak elkerülése érdekében, túlcsorduló forraszanyag tetszőleges offset összetevők és egyéb forrasztási hibák nem tudja megakadályozni elrendezése viák a párna vagy elemek azok közvetlen közelében. Mint már említettük, az szükséges, hogy az érintkező felületeket komponenseket elválasztottuk az átvezetéseket, párna és más stb forrasztósabionhoz.
Ez a szabály nagyon fontos a chipek alacsony pályán - az érintkezési felületeket kell elválasztani egy maszkot. Sami átvezetésekről található a közvetlen közelében a párna, kívánatos, hogy lezárja a forrasztósabionhoz.
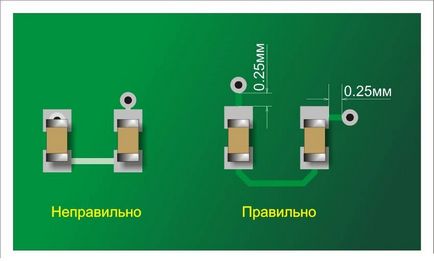
Elemek belsejében található sokszögek el kell különíteni azoktól a termikus akadályokat. Ezzel elkerülhető egyenetlen felmelegedés különböző párna az azonos összetevő forrasztás során, és ennek következtében az elmozdulás ezen eleme, a „hideg forrasztási” hibák „sírkő” és a t. D.
Az is kívánatos, hogy csatlakoztassa a érintkező felületeket és széles vezetékek nem közvetlenül, hanem szűk karmester. A paraméterek ezen összekötő-vezeték függően választjuk jelenlegi áthalad rajta. Ezzel elkerülhető a „hideg forrasztási” hatást.
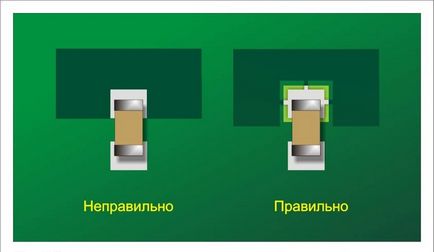
Az egyik legfontosabb szempont a tervezés nyomtatott áramköri szerelvények a betartását formák és méretek a párna. Eltérés ezen paraméterek gyakran vezet mellékhatások, mint a hatása „sírkő” vagy „szalag”, az egyik terminál nepropay komponens, nincs kapcsolat a forrasztott kötés, elfogadhatatlanul nagy elmozdulás elem. Ezért a tervezés a termék figyelembe kell venni az ajánlásokat a gyártók az alkatrészek, hogy használják a leírások, valamint a leggyakrabban használt összetevők - IPC és a JEDEC szabványoknak, különösen az új IPC-7351A szabvány szabályozza a méret a párna, és egyéb paraméterek a nyomtatott áramköri szerelvények, amelyek kritikusak a felszíni board szerelés .
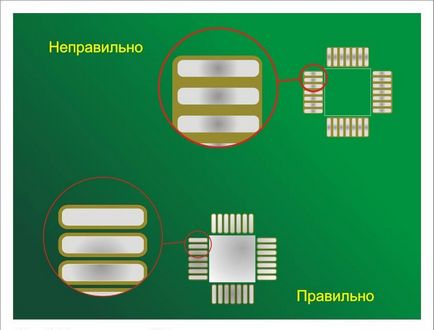
Chipek BGA csomag
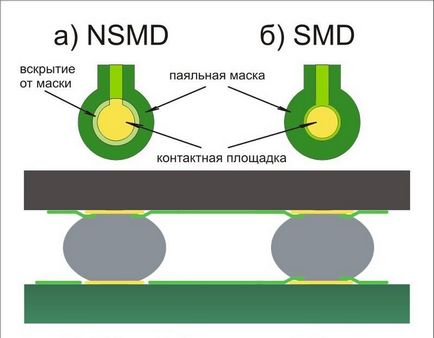
Egy első kiviteli alaknál nagyobb erőt a forrasztott kötés, mivel a nagyobb érintkezési felület és a kapcsolatot az oldalán a leszállás pad, ahogyan ez a legjobban központosító komponens, és sokoldalúbb és technológiailag valamint szerelési gyártásához nyomtatott áramköri lapok.
Az előnye, hogy a második kiviteli alak az, hogy növelje meg a kötés szilárdságát pad maga és a PCB dielektromos. Ennek használata indokolt, ha a további menetében összeszereléshez, teszteléshez, illetve működését a díj tárgya lehet hajlítások vagy más fizikai igénybevétel, valamint a működés során magas hőmérséklet-változás, vagy ha a termék lesz nagyon szigorú termikus tesztelése.
Ha a gyártó nem különleges utasításokat a helyszínen típusú, akkor ajánlott alkalmazni NSMD típusát.
A jellemzője BGA chipek az, hogy a következtetések alá rejtett a szervezetben, ami megnehezíti, hogy ellenőrizze a minőségét telepítést. A fő vizsgálati eszközei forrasztott kötések ilyen chipekkel fluoroszkópiai útmutatást. De ebben az esetben, néhány hibája, mint a még nepropay bizonyos következtetéseket lehet nehéz felismerni. Annak érdekében, hogy növelje a hatékonyságát a kontroll a forrasztás chips ajánlatos csatolni a párna egy speciális formája (6. ábra).
Amikor ilyen párnák forrasztott csatlakozás formáját ölti egy jellemző, amely nagymértékben javítja a klinikai teszt, különösen egy automatikus üzemmódban.
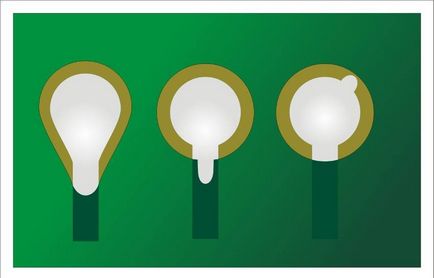
referencia jel
Minden kártyán van szükség, hogy a jelenléte legalább három referencia jelek fenntartásához szükséges az automatizálási rendszerek.
Kiindulási pontok kell lennie egy kör alakú pad egy 1 mm átmérőjű, nyitott a maszk egy 3-4 mm átmérőjű. (7. ábra)
Ezeket úgy kell elhelyezni a sarkokban a fedélzeten (de aszimmetrikusan), és hogy olyan távol egymástól (8. ábra).
Kívánatos, vezetékek, érintkező felületeket, átmeneti, szerelési lyukak és egyéb elemek a nyomtatott áramköri lap található legalább 5 mm-re a központtól a kiindulási pontok.
Ha a tábla nem elég hely a referencia jelek, ki kell őket helyezni a technológiai területen, ami maga után vonja növekedett a terület (9. ábra).
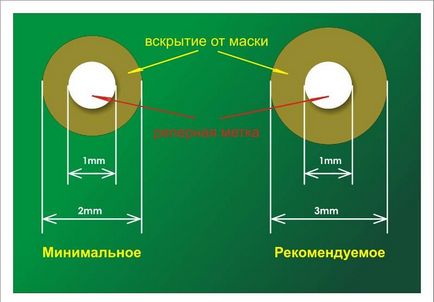
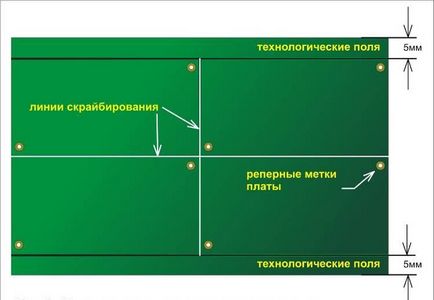
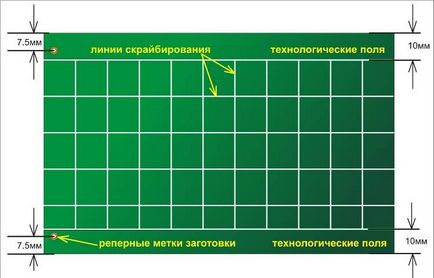
Ha a tábla elhelyezésére nagy fém sokszögek, előnyösen ezt mindkét oldalán a fedélzeten lehetőleg egyenletesen, és elvégzik a rács vezetékek. Ez megakadályozza deformáció a fedélzeten a gyártás során és összeszerelés, amikor melegítjük újrafolyató kemencében.
Ruha mérete és a csoport üres
technológiai területen
A berendezés lehetővé teszi a szerelvény egyéni vagy csoportos ellátás nélküli vak speciális technológiai lyukak és a mezők. Azonban ebben az esetben a hosszú oldalán a fedélzeten komponensek kell elhelyezni nem közelebb, mint 5 mm-re a szélétől. Ha a felület szerelt alkatrész elhelyezve mindkét oldalán a fórumon, ez a szabály tiszteletben kell tartani, és a második oldalon. Egyébként a hosszú oldalon a fórumon, vagy multizagotovki kell befogadni a technológiai területen 5 mm széles.
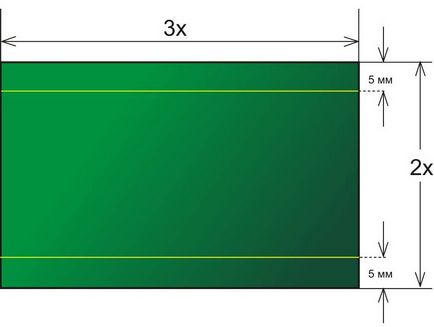
Válás fedélzeten üres
Két elválasztási módszerei táblák közte és technológiai területeken: előrajzolásához és maró a kontúr mentén a fórumon. Az első esetben, az egyenes vonalak táblák és alkalmazott területeken részén darabok, hogy hagyja el ezeken a helyeken a jumper, amelynek mérete meghatározza a merevséget az egész munkadarab egészét, valamint az azt követő elválasztás egyszerűsége. Ha az asztalon lesz telepítve automata vonalak, vastagabb áthidaló (Ris.11a), hogy nagyobb merevséget munkadarab egészét. Elválasztására táblák később használt speciális eszközök, ne hozzon feszültségterhelések az áramköri lapon.
A kézi telepítés és elkülönítése ezen jumperek készülnek lényegesen vékonyabb (fig.11b), amely lehetővé teszi a könnyű kézi szétválasztás anélkül, az alaplap vagy forrasztott termékeket.
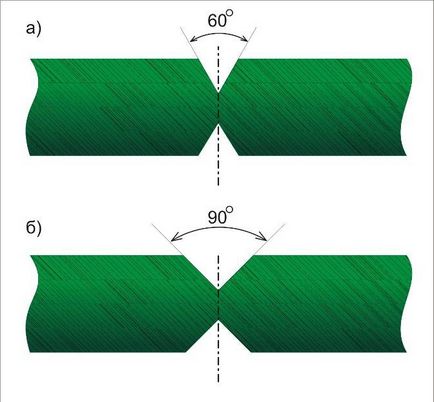
Ha a nyomtatott áramkör egy bonyolult vagy nem igényelnek nagy minőségű és pontos feldolgozása e hurok, a szétválás végezzük őrléssel táblák képeznek közötti hidak a táblák és a területeken, amelyeken azok együttes a munkadarabba (12. ábra). Szélei mentén a hidak egy sor lyuk, hogy megkönnyítse azok későbbi szétválasztása.
Ilyen esetekben szükséges, hogy egy áramköri tér legalább 3-4 ilyen jumper.
Hasonló módszert is kell alkalmazni olyan esetekben, amikor a táblák vannak telepítve a felületre szerelt csatlakozók (USB, SIM, memóriakártyák, stb), a méretei, amelyek kívül esnek a szélén a tábla. Ellenkező esetben a bejelentést az előrajzolásához, a helyes felosztása tuskó a speciális berendezések lehetetlen lesz.
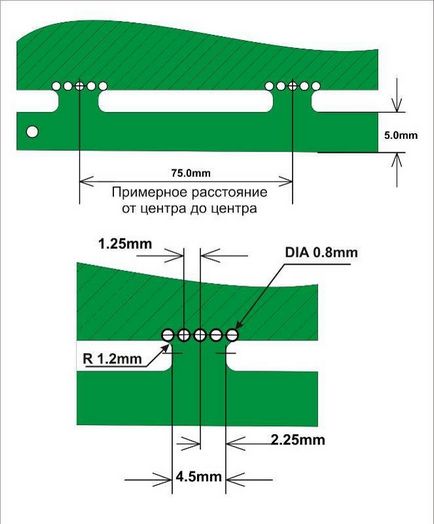
befejezi
Modern PCB gyártási technikák lehetőséget nyújtanak a kiválasztási egy végső bevonatot függően változnak e vagy más jellemzőket, vagy paramétereket a termék. Ebben a részben fogjuk érinteni bizonyos tulajdonságait a leggyakoribb felületekről, amelyek tükröződnek a telepítés termékeket.
A legnépszerűbb ma a bevonat alapuló ón-ólom ötvözet (PIC-63). Az alkalmazás módja és kiegyenlítés a forraszanyag felületén a érintkező felületeket, és a kitett részei réz nevezett HASL (vagy HAL) - Hot Air Solder Szintbeállító, azaz forró levegő forrasztani kiegyenlítése. Ez a bevonat hosszú és jól ki magát köszönhetően a kiváló forraszthatóság, forrasztott kötések nagy szilárdságú, hosszú fennmaradásával tulajdonságok forrasztás előtt, nagy karbantarthatóság szerelvények az ilyen borítással. Ez a bevonat azonban jelentős simaság és egyenetlen bevonat vastagsága az érintkező szigeteken a különböző méretű és orientáció, amelyek problémákat okozhatnak a szerelvény számos fejlett alkatrészek, mint a BGA, QFN, alkatrészek a hővezető tű alatt a ház és a komponensek a kis-pályán.
Ha az ilyen komponensek vannak jelen a nyomtatott áramkör, a végső bevonat jobb választani az egyik az úgynevezett merítés bevonat: ENIG (elektrolitikus nikkel / bemerítés arany, néha említett ImAu) - elektrolitikus nikkel / bemerítés arany, ImSn - immerziós ón, IMAG - immerziós ezüst. Segítségével az ilyen bevonatok a NYÁK-on érintkező felületeket kapjunk tökéletesen sima, ami megkönnyíti alkatrész-összeszerelés golyós csap, ólommentes alkatrészek és egyéb modern épületek.
Az előnyök a merülő aranyozás egy jó forraszthatóság, arany jól oldódik forraszanyag és a nem érintett gyorsan tarnish és oxidációs, magas bevonat tartósságát. Immersion ezüst - viszonylag drága és nagyon tech bevonat kiváló forraszthatóság és nagy szilárdságú forrasztott kötések. Kiváló bevonat előállítására billentyűzetek és érintőképernyők. Bemerítés ón bevonat jól alkalmazható összekötő lapok, valamint amiatt, hogy a vastag bevonat és egy jó csúszófelület talán a legjobb fedél szerelési csatlakozók Press-Fit technológia.
Fontos megjegyezni, hogy az összes ilyen típusú bevonatok, továbbá a HASL, megfelelnek a RoHS irányelv korlátozását célzó ólom az elektronikai iparban, és alkalmasak ólommentes forrasztás. Továbbá, az utóbbi években terjedt el a szerves védőbevonat - OSP - szerves forraszthatóság tartósítószer. A fő különbség a fent leírt eljárásokkal az, hogy ahelyett, hogy közvetlenül a réz fém betét elhelyezett szerves réteg, amely védi a rezet az oxidációtól. Amikor forrasztás, ez a réteg teljesen feloldódik. Ez a bevonat, mint a többi más, számos hátránya van: rövid távú tárolása a forrasztás előtt, forraszthatóság alábbiakban a fenti, ez nem ajánlott a nagy termékek, a jelenléte egy nem-vezető réteg problémát okozhatnak a villamos-áramkör tesztelési, stb De egyes források szerint az erejét forrasztott kötések ezen bevonatok, még nagyobb, mint HASL-bevonat és merülő arany. A sík a párna, amely a OSP, nagyon magas, így ez a borító tökéletes beállítására BGA típusú alkatrészek, ólommentes alkatrészek és komponensek alacsony hajlásszögű.
Annak ellenére, hogy a követelmények az RoHS irányelv Magyarországra nem vonatkozik, azok közvetett hatása a magyar termelőknek. Tehát sok gyártó az elektronikus alkatrészek, vagy teljesen áttért a termelés alkatrészek ólommentes vezet, vagy fokozatos átmenet ilyen. Most ez gyakran nagyon nehéz felszerelni egy adott termék csak a hagyományos, vagy csak ólommentes alkatrészeket. Bár a telepítés két említett és egyéb alkatrészek nem teljesen korrekt, néha egyszerűen nem lehet elkerülni, de a használata révén a megfelelő anyagok és eljárási paraméterek ilyen esetekben is lehetséges, hogy olyan stabil minőségű forrasztás.